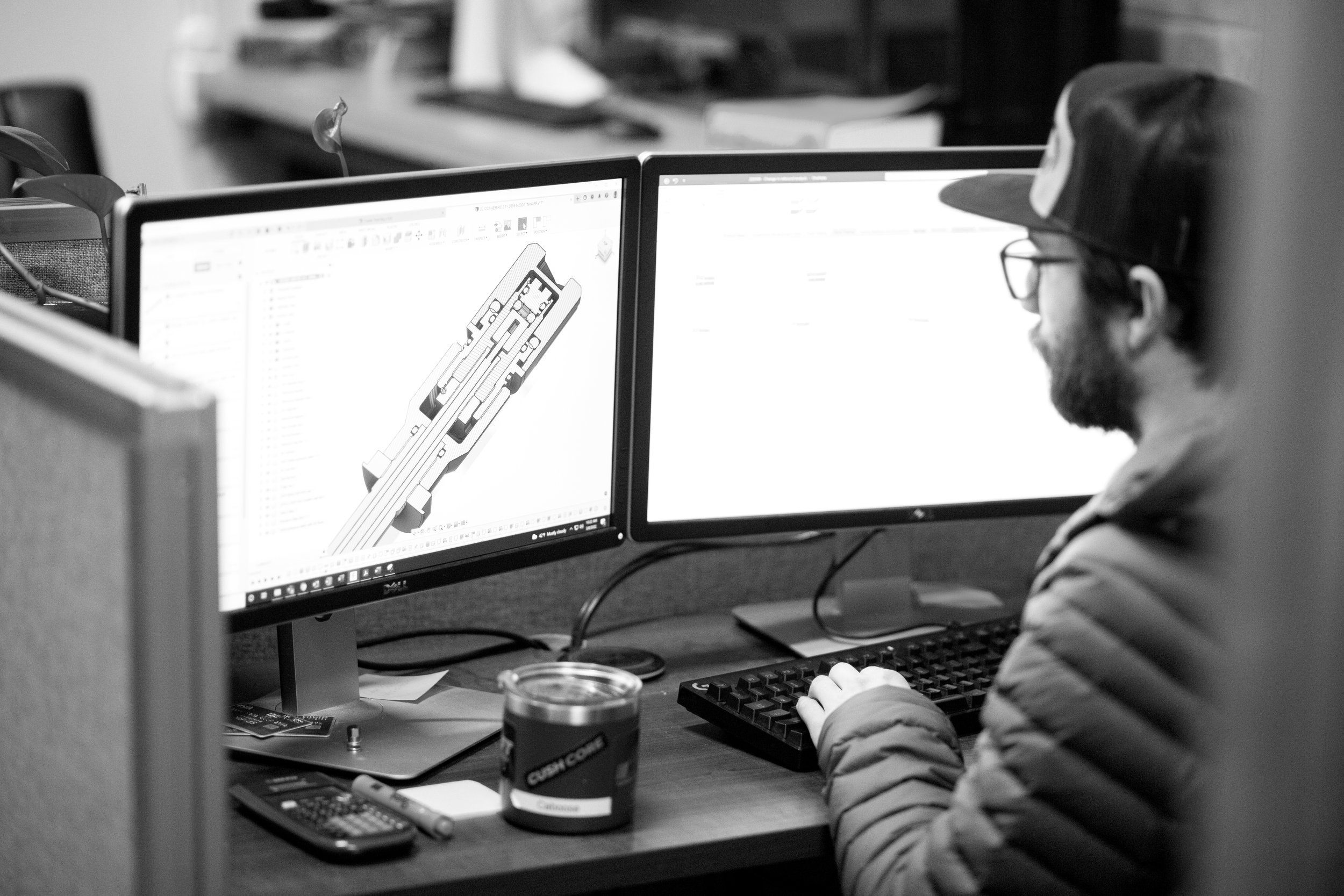
SUSPENSION ENGINEERING
Data-driven suspension solutions, personalized for you.
research & development
Kreft Moto uses a scientific approach to suspension engineering. Almost from the beginning we’ve used the MTS Roehrig EMA-2K dynamometer to analyze, diagnose, and tune suspension. More recently we’ve added Motion Instrument’s (MI) data acquisition equipment to our arsenal. With these tools we can collect accurate, objective data. This approach separates Kreft Moto from the “garage tuner” and, most importantly, delivers better performance and a better experience for our customers.
Suspension lab & machine shop
Suspension dynamometer
Kreft Moto’s suspension dynamometer (AKA Dyno) is a powerful tool which separates us from other tuners. This machine and accompanying analysis software allow us to quantitatively characterize damper performance with extreme precision and detail. Our dyno can accelerate beyond 120 G’s and achieve velocities up to 4000 mm/s. This broad range of testing capabilities allows us to accurately and consistently simulate both common and extreme events your suspension might encounter while riding. Learning from this data, we create the perfect damping curve for your riding terrain, style, skill, and preference.
cnc machines
Here at Kreft Moto, we not only custom tune suspension for a better riding experience, we machine components for improved performance too! We have a Tormach CNC lathe and vertical mill in our machine shop. Using these machines, we modify OEM suspension parts to achieve preferred performance characteristics, adding value and saving the customer money. During the suspension design and development process, we machine functional prototypes for qualitative ride performance and suspension durability testing on the track and trail.
3d printers
As part of Kreft Moto’s research and development program, in-house engineers utilize 3D-printers to rapid prototype parts. Rapid prototyping allows us to quickly iterate designs and improve our part and performance upgrades for WP forks and shocks. Kreft Moto has both filament based FDM and resin based SLA 3D-printers giving us the right tools and engineering grade materials for any project. The parts we print allow us to check fitment, refine shape and feel, and occasionally test functional suspension prototypes. Design concepts are printed, tested, and refined until we achieve our desired suspension feel, function, and adjustability. We develop suspension settings for new OEM models faster than other tuners by using these machines and development processes.
Manual Lathes & MIlls
In our machine shop, we have a vertical Bridgeport mill and two manual lathes at our engineer’s fingertips so they can experiment with things like: material weight savings, surface finishes, and formation of custom one-off parts. For individual parts and modifications these manual machines save time and allow us to create functional metal prototypes with ease. We also utilize these machines to make jigs and fixture for testing, quality control, and improve our manufacturing and assembly methods.
3d CAD & Engineering Software
During the development and creation of Kreft damping components and hardparts we utilize Fusion 360 as our CAD package. It allows us to quickly create, modify, and assemble parts virtually before moving to production. We also use the built in tools for developing CNC toolpaths for prototyping. Finally, we can simulate parts under the loads they will experience in the field. This is particularly useful for identifying and alleviating stress concentrations in critical damper components. We also utilize Restackor, a damper modeling tool, to simulate shimstack changes before implementation in real shocks. This tool isn’t a perfect representation of the real world but can save valuable time and reduce the number of iterations it takes to get each customer the perfect damping curve.